Disposal of pentane in EPS foam manufacturing facilities
Otto Plettner, Epsilon Holdings, LLC, Glendora, CA, USA
Although the topic “disposal of pentane“ has been around for approximately 20 years in the EPS processing industry, up to now little has been done about it in Europe. Even though the contribution of pentane emissions from EPS processing plants to the environment is small in comparison to VOC emissions from other sources, it can be assumed that in the foreseeable future the EPS processing industry in Europe will have to take a clear position with respect to this issue.
Regrettably, this question was not always handled in the past by qualified and responsible persons. The few EPS processing facilities in Europe, in which projects for the disposal of pentane emissions were carried out, are in most cases outfitted with systems that do not show advanced technology and were set up under high expenses. Consequently, the issue of disposal of pentane emissions in the EPS foam process is met within the EPS industry with skepticism and regarded as an unreasonable burden.
In this presentation various aspects of pentane disposal are analyzed objectively, trying to make a contribution for a correct assessment of this issue, not only within the EPS processing industry but also among bodies in charge of air pollution control. Based on its findings, technically feasible and economically justifiable possibilities for the reduction of pentane emissions are presented and discussed.
1. Background
The topic "pentane disposal" became an issue in the USA during the late 1980ies and early 1990ies, when important additions to the Clean Air Act" [1], [2] of 1970 were passed. Among other things, pentane was classified as VOC (Volatile Organic Compound), making the emission of pentane to be subject to environmental regulations. Particularly the EPS processing plants located in the area around Los Angeles, California were requested to take measures to control their pentane emissions, due to the fact that this area had the highest air pollution in the USA.
Some of the EPS converters tried, without success, to fight the application of the new regulations with legal means and through their trade associations. Despite the changes in the political direction, which took place since that time in the USA at the Federal Government and Regional levels, these regulations became rather more stringent in some areas.
The classification of pentane as a VOC is related to the formation of Ozone in the troposphere (i.e. at ground level; not to be mixed up with Ozone in the Stratosphere!). The formation of Ozone at ground level results from chemical reactions, in presence of sunlight, between VOCs and nitrogen oxides (NOx - which are given off in any combustion process). Something similar happens with unburned fuels in the exhaust gases of automobiles and trucks which, by the way, contribute substantially more to air pollution than the pentane emissions from EPS processing plants.
2. Past developments
Since introduction in the USA of the above-mentioned regulations for clean of air, each area in which the maximum values of Ozone in air (average over 8 hours: 0.08 ppm, [3]) are constantly surpassed (“non attainment areas” [4]) the emission of pentane (and other VOCs) is subject to regional and/or local air pollution control regulations. Thus many of the American EPS processing plants fall under these regulations and are made responsible for an appropriate reduction and disposal of their pentane emissions.
In the 1990ies several EPS processing plants in the USA were outfitted with pentane emission control systems. Unfortunately, sometimes companies and/or persons also took part in such projects who, as it turned out later, used the limited knowledge of officials at the corresponding regulating bodies and acted in a way which resembled more a trade with the corresponding permits, rather than a technically sound solution of the intended task of air pollution control. This had as a consequence that in recent years particularly the EPA (Environmental Protection Agency) found, through random inspections of facilities with authorized pentane emission control systems, that the latter fulfilled their purpose only partially, if at all. Thus, a stricter control of all EPS processing facilities that are subject to environmental approval is now taking place.
Some of the affected EPS converters now argue that the environmental authorities often show an authoritarian attitude and little understanding for the EPS industry, and that the requirements contained in various VOC regulations are not attainable. Some EPS converters have even opted to relocate their facilities abroad.
Among the enacted environmental regulations addressing pentane emissions from EPS processing plants, Rule 1175 [5] of the South Coast Air Quality Management District (SCAQMD) in the southern part of California shall be mentioned here.
According to it, EPS processing plants may emit to the environment a maximum of 2.4% pentane, based on the quantity of the EPS raw material processed. However this limit also includes the residual pentane content of the finished product coming out of the molding tool.
Concerning the issue of pentane disposal in EPS processing plants in Europe, the following measures and/or developments, among others, might be of importance:
In Switzerland, based on the decree: "Regulation on the Control of Volatile Organic Compounds” of November 1997 [6], a fee of CHF 3. - /kg VOC is raised, which can be refunded after submittal of an appropriate “VOC Balance” of the corresponding production site.
The European Environmental Agency (EEA) adopted in October of 2000 the guideline: COM(2000)613final [7], according to which, starting in the year 2010, the Ozone content in air may not exceed 120μg/m3 over 8 hours and during less than 26 days/year (approx. 30% less than the current limit in the USA of 0.08 ppm).
The guideline: 2002/3/EG of Feb. 2, 2002 of the European Parliament and Council [8] over the Ozone content in air, prescribes, in order to reach the goal values for Ozone, measurements on Ozone precursors among which pentane is also expressly mentioned.
3. Contribution of EPS pentane emissions to total VOC emissions
In most discussions on pentane emissions from EPS processing plants, it remains often unmentioned how much the emission of pentane to the environment actually represents, as compared to VOC emissions from other sources.
Through a closer examination, it can be seen that the contribution of EPS to total VOC emissions is very small.
Table 1: VOC emissions in the USA during the year 2003 [9]
* Estimated
** An average pentane content of 6% is assumed.
From these data it can be seen that if, for instance, VOC emissions from mobile sources (i.e. mainly motor vehicles) would be lowered by only 1%, a substantially bigger improvement of the air quality could be achieved than with a 100% elimination of all pentane emissions from EPS processing plants.
However, it should also be noted that since 1970, total VOC emissions in the USA were reduced by approx. 50%, while pentane emissions from EPS processing increased since then by the same amount as the EPS consumption.
Table 2: VOC emissions in Europe * in the year 2003 [11]
* 25 countries
** Estimated
*** An average pentane content of 6% is assumed .
VOC emissions in Europe were reduced between 1990 and 2003 approx. 41.5%, while in the same period in the USA these were reduced approx. 33.3%. Based on these data, it can be concluded that the contribution of EPS to total VOC emissions is, though even still small, more critical in Europe than in the USA.
4. Pentane as expanding agent for EPS
Ever since EPS was developed, predominantly, almost exclusively, pentane has been used as its expanding agent (with approx. 6 %, based on EPS weight). Mainly n-pentane (see table 3) was, and still is, used. Various EPS raw material manufacturers add some Iso-pentane and recently some also add Cyclopentane. All these pentane isomers cause the same reactions in air (Ozone formation) and therefore are treated all as VOCs by environmental authorities.
When the topic "pentane disposal” became an issue, several raw material manufacturers developed and offered to the EPS converters raw material types with lower pentane content (3.5 - 4.5%). Reductions in pentane emissions of up to 40% (or 25%) can thereby be achieved; however, it must be acknowledged that with 3.5% the lowest limit in content of expanding agent for EPS has probably been reached.
Recently a report appeared according to which a water-foamable EPS (WEPS) has been developed [13].
Although this development could solve the problem of pentane disposal in EPS processing completely, the blowing capacity of water has to be considered carefully. If one compares the values of Table 4 (see below) with those from Table 5, it follows that in the temperature range of the EPS foam process (90°C - 110°C) water has only 15 - 20% of the vapor pressure of pentane. Therefore, water can hardly replace pentane as an expanding agent for conventional EPS.
It remains to be seen whether further developments in this direction will bring out an EPS type than can be processed easily and which can also compete economically against other insulating and packing materials.
5. Physical and chemical properties of pentane
Table 3: Pentane isomers that are used as expanding agents for EPS
Of the properties of pentane, the following are particularly important for emission control:
Density; pentane vapor is 2,5 times heavier than air [15]
Vapor pressure.
Table 4: Vapor pressure of pentane [16]
Explosive range.
Lower explosive limit: 1.5% by volume in air [15]
Upper explosive limit: 7.8% by volume in air [15]
Outside these limits, air pentane mixtures are not ignitable.
Heat of combustion.
n-pentane: 45.0 MJ/kg or 136.959 MJ/m3 [18]
(methane: 50.1 MJ/kg or 33.818 MJ/m3) [18]
6. Points of emission in the EPS process
The most important points of pentane emission in the EPS process are, in order of importance:
Pre-expansion
Aging storage of the pre-expanded EPS
Molding
Degassing the finished EPS foam product
Table 6 Pentane losses in the EPS foam process *
* Approx. averages, in % of the original pentane content
Erroneously, sometimes the following steps of the EPS process are considered to be emission sources:
Opening of the raw material containers.
As long as the containers are opened only on their upper side and not exposed to any air current, the pentane vapor in the container can hardly escape because, due to its density, it behaves practically like a liquid.
Drying in the fluidized bed.
After pre-expansion, the EPS beads are exposed in the fluidized bed to a certain cooling, which makes pentane emission in this step impossible. However, it can occur that some pentane from the pre-expander is carried into the fluidized bed; this must be taken into account when planning and starting-up an emission control system.
Fresh foamed products.
Immediately after molding, no emission of the residual pentane of the finished EPS foam product can take place. Fresh finished EPS foam products actually have an internal negative pressure which, depending of their wall thickness, needs up to several hours to disappear, and only afterwards does the degassing of the residual pentane content actually begin.
Although the topic “disposal of pentane“ has been around for approximately 20 years in the EPS processing industry, up to now little has been done about it in Europe. Even though the contribution of pentane emissions from EPS processing plants to the environment is small in comparison to VOC emissions from other sources, it can be assumed that in the foreseeable future the EPS processing industry in Europe will have to take a clear position with respect to this issue.
Regrettably, this question was not always handled in the past by qualified and responsible persons. The few EPS processing facilities in Europe, in which projects for the disposal of pentane emissions were carried out, are in most cases outfitted with systems that do not show advanced technology and were set up under high expenses. Consequently, the issue of disposal of pentane emissions in the EPS foam process is met within the EPS industry with skepticism and regarded as an unreasonable burden.
In this presentation various aspects of pentane disposal are analyzed objectively, trying to make a contribution for a correct assessment of this issue, not only within the EPS processing industry but also among bodies in charge of air pollution control. Based on its findings, technically feasible and economically justifiable possibilities for the reduction of pentane emissions are presented and discussed.
1. Background
The topic "pentane disposal" became an issue in the USA during the late 1980ies and early 1990ies, when important additions to the Clean Air Act" [1], [2] of 1970 were passed. Among other things, pentane was classified as VOC (Volatile Organic Compound), making the emission of pentane to be subject to environmental regulations. Particularly the EPS processing plants located in the area around Los Angeles, California were requested to take measures to control their pentane emissions, due to the fact that this area had the highest air pollution in the USA.
Some of the EPS converters tried, without success, to fight the application of the new regulations with legal means and through their trade associations. Despite the changes in the political direction, which took place since that time in the USA at the Federal Government and Regional levels, these regulations became rather more stringent in some areas.
The classification of pentane as a VOC is related to the formation of Ozone in the troposphere (i.e. at ground level; not to be mixed up with Ozone in the Stratosphere!). The formation of Ozone at ground level results from chemical reactions, in presence of sunlight, between VOCs and nitrogen oxides (NOx - which are given off in any combustion process). Something similar happens with unburned fuels in the exhaust gases of automobiles and trucks which, by the way, contribute substantially more to air pollution than the pentane emissions from EPS processing plants.
2. Past developments
Since introduction in the USA of the above-mentioned regulations for clean of air, each area in which the maximum values of Ozone in air (average over 8 hours: 0.08 ppm, [3]) are constantly surpassed (“non attainment areas” [4]) the emission of pentane (and other VOCs) is subject to regional and/or local air pollution control regulations. Thus many of the American EPS processing plants fall under these regulations and are made responsible for an appropriate reduction and disposal of their pentane emissions.
In the 1990ies several EPS processing plants in the USA were outfitted with pentane emission control systems. Unfortunately, sometimes companies and/or persons also took part in such projects who, as it turned out later, used the limited knowledge of officials at the corresponding regulating bodies and acted in a way which resembled more a trade with the corresponding permits, rather than a technically sound solution of the intended task of air pollution control. This had as a consequence that in recent years particularly the EPA (Environmental Protection Agency) found, through random inspections of facilities with authorized pentane emission control systems, that the latter fulfilled their purpose only partially, if at all. Thus, a stricter control of all EPS processing facilities that are subject to environmental approval is now taking place.
Some of the affected EPS converters now argue that the environmental authorities often show an authoritarian attitude and little understanding for the EPS industry, and that the requirements contained in various VOC regulations are not attainable. Some EPS converters have even opted to relocate their facilities abroad.
Among the enacted environmental regulations addressing pentane emissions from EPS processing plants, Rule 1175 [5] of the South Coast Air Quality Management District (SCAQMD) in the southern part of California shall be mentioned here.
According to it, EPS processing plants may emit to the environment a maximum of 2.4% pentane, based on the quantity of the EPS raw material processed. However this limit also includes the residual pentane content of the finished product coming out of the molding tool.
Concerning the issue of pentane disposal in EPS processing plants in Europe, the following measures and/or developments, among others, might be of importance:
In Switzerland, based on the decree: "Regulation on the Control of Volatile Organic Compounds” of November 1997 [6], a fee of CHF 3. - /kg VOC is raised, which can be refunded after submittal of an appropriate “VOC Balance” of the corresponding production site.
The European Environmental Agency (EEA) adopted in October of 2000 the guideline: COM(2000)613final [7], according to which, starting in the year 2010, the Ozone content in air may not exceed 120μg/m3 over 8 hours and during less than 26 days/year (approx. 30% less than the current limit in the USA of 0.08 ppm).
The guideline: 2002/3/EG of Feb. 2, 2002 of the European Parliament and Council [8] over the Ozone content in air, prescribes, in order to reach the goal values for Ozone, measurements on Ozone precursors among which pentane is also expressly mentioned.
3. Contribution of EPS pentane emissions to total VOC emissions
In most discussions on pentane emissions from EPS processing plants, it remains often unmentioned how much the emission of pentane to the environment actually represents, as compared to VOC emissions from other sources.
Through a closer examination, it can be seen that the contribution of EPS to total VOC emissions is very small.
Table 1: VOC emissions in the USA during the year 2003 [9]
VOC emissions, total: | 13.995.000 t = 100% |
VOC emissions from mobile sources: | 6.349.000 t = 45% |
VOC emissions from stationary sources: | 7.646.000 t = 55% |
EPS consumtion in the USA in 2003 * [10]: | 405.000 t |
EPS VOC emissions ** : | 24.300 t = 0,17% |
** An average pentane content of 6% is assumed.
From these data it can be seen that if, for instance, VOC emissions from mobile sources (i.e. mainly motor vehicles) would be lowered by only 1%, a substantially bigger improvement of the air quality could be achieved than with a 100% elimination of all pentane emissions from EPS processing plants.
However, it should also be noted that since 1970, total VOC emissions in the USA were reduced by approx. 50%, while pentane emissions from EPS processing increased since then by the same amount as the EPS consumption.
Table 2: VOC emissions in Europe * in the year 2003 [11]
VOC emissions, total: | 9.621.230 t = 100% |
EPS consumption in Europe in 2003 ** [12]: | 774.000 t |
EPS VOC emissions ***: | 46.440 t = 0,48% |
** Estimated
*** An average pentane content of 6% is assumed .
VOC emissions in Europe were reduced between 1990 and 2003 approx. 41.5%, while in the same period in the USA these were reduced approx. 33.3%. Based on these data, it can be concluded that the contribution of EPS to total VOC emissions is, though even still small, more critical in Europe than in the USA.
4. Pentane as expanding agent for EPS
Ever since EPS was developed, predominantly, almost exclusively, pentane has been used as its expanding agent (with approx. 6 %, based on EPS weight). Mainly n-pentane (see table 3) was, and still is, used. Various EPS raw material manufacturers add some Iso-pentane and recently some also add Cyclopentane. All these pentane isomers cause the same reactions in air (Ozone formation) and therefore are treated all as VOCs by environmental authorities.
When the topic "pentane disposal” became an issue, several raw material manufacturers developed and offered to the EPS converters raw material types with lower pentane content (3.5 - 4.5%). Reductions in pentane emissions of up to 40% (or 25%) can thereby be achieved; however, it must be acknowledged that with 3.5% the lowest limit in content of expanding agent for EPS has probably been reached.
Recently a report appeared according to which a water-foamable EPS (WEPS) has been developed [13].
Although this development could solve the problem of pentane disposal in EPS processing completely, the blowing capacity of water has to be considered carefully. If one compares the values of Table 4 (see below) with those from Table 5, it follows that in the temperature range of the EPS foam process (90°C - 110°C) water has only 15 - 20% of the vapor pressure of pentane. Therefore, water can hardly replace pentane as an expanding agent for conventional EPS.
It remains to be seen whether further developments in this direction will bring out an EPS type than can be processed easily and which can also compete economically against other insulating and packing materials.
5. Physical and chemical properties of pentane
Table 3: Pentane isomers that are used as expanding agents for EPS
Isomer | Formula | Boiling point |
n-pentane | CH3 – ( CH2 )3 – CH3 | 36.1 °C [14] |
Iso-pentane | CH3 – CH( CH3 ) – CH2 – CH3 | 28.0 °C [14] |
Cyclopentane | CH2CH2CH2CH2CH2 | 49.0 °C [14] |
Of the properties of pentane, the following are particularly important for emission control:
Density; pentane vapor is 2,5 times heavier than air [15]
Vapor pressure.
Table 4: Vapor pressure of pentane [16]
Temperature: | 36 °C | 50 °C | 70 °C | 90 °C | 110 °C |
(Torr) | 44.6 | 92.5 | 233.7 | 525.8 | 1,075 |
(bar) | 0.059 | 0.123 | 0.312 | 0.701 | 1.433 |
Explosive range.
Lower explosive limit: 1.5% by volume in air [15]
Upper explosive limit: 7.8% by volume in air [15]
Outside these limits, air pentane mixtures are not ignitable.
Heat of combustion.
n-pentane: 45.0 MJ/kg or 136.959 MJ/m3 [18]
(methane: 50.1 MJ/kg or 33.818 MJ/m3) [18]
6. Points of emission in the EPS process
The most important points of pentane emission in the EPS process are, in order of importance:
Pre-expansion
Aging storage of the pre-expanded EPS
Molding
Degassing the finished EPS foam product
Table 6 Pentane losses in the EPS foam process *
Phase | Pentane loss |
Pre-expansion: Aging storage: Molding: |
25 – 40% 20 – 35% 10 – 20% |
Total process: | 65 – 85% |
Residual pentane: | 15 – 35% |
Erroneously, sometimes the following steps of the EPS process are considered to be emission sources:
Opening of the raw material containers.
As long as the containers are opened only on their upper side and not exposed to any air current, the pentane vapor in the container can hardly escape because, due to its density, it behaves practically like a liquid.
Drying in the fluidized bed.
After pre-expansion, the EPS beads are exposed in the fluidized bed to a certain cooling, which makes pentane emission in this step impossible. However, it can occur that some pentane from the pre-expander is carried into the fluidized bed; this must be taken into account when planning and starting-up an emission control system.
Fresh foamed products.
Immediately after molding, no emission of the residual pentane of the finished EPS foam product can take place. Fresh finished EPS foam products actually have an internal negative pressure which, depending of their wall thickness, needs up to several hours to disappear, and only afterwards does the degassing of the residual pentane content actually begin.
7. Methods for controlling pentane emissions.
In principle, any pentane disposal system consists of 2 parts:
• The system to capture (collect) the pentane emissions
• The control unit for the actual disposal of the captured pentane emissions.
There are several alternatives for capturing pentane emissions:
A simple collecting line.
At each point of emission fresh air is drawn into a main collecting line (pipe and/or duct) and sent to the control unit. Thus, a relatively large air flow is created in which the pentane emissions become very diluted. Therefore, the corresponding control unit must have an equivalent large capacity (approx. 7,500 m3/h for a throughput of 1 t/h EPS).
In principle, any pentane disposal system consists of 2 parts:
• The system to capture (collect) the pentane emissions
• The control unit for the actual disposal of the captured pentane emissions.
There are several alternatives for capturing pentane emissions:
A simple collecting line.
At each point of emission fresh air is drawn into a main collecting line (pipe and/or duct) and sent to the control unit. Thus, a relatively large air flow is created in which the pentane emissions become very diluted. Therefore, the corresponding control unit must have an equivalent large capacity (approx. 7,500 m3/h for a throughput of 1 t/h EPS).
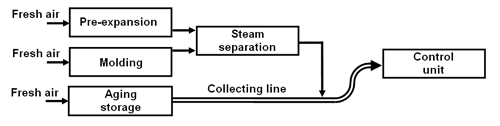
Fig. 1: Simple collecting line (schematic diagram).
Closed collection circuit.
In this system, the emissions are brought into a collection circuit. Pentane-laden air is taken out of the collection circuit and supplied to the control unit. The pentane-laden air taken out of the collection circuit is replaced with fresh air. The emitted pentane is diluted with fresh air only within the aging storage. That makes it possible to handle smaller amounts of air with higher pentane concentration and allows the use of smaller control units (approx. 2,500 m3/h for a throughput of 1 t/h EPS).
In this system, the emissions are brought into a collection circuit. Pentane-laden air is taken out of the collection circuit and supplied to the control unit. The pentane-laden air taken out of the collection circuit is replaced with fresh air. The emitted pentane is diluted with fresh air only within the aging storage. That makes it possible to handle smaller amounts of air with higher pentane concentration and allows the use of smaller control units (approx. 2,500 m3/h for a throughput of 1 t/h EPS).
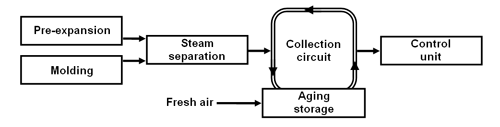
Fig. 2: Closed collection circuit (schematic diagram).
Ventilated production building
This alternative does not require a special collecting mechanism to capture the emitted pentane, since all emissions can be caught in the (hermetic) production building. However, the pentane concentration may not exceed the max. allowable concentration in working areas (600 ppm, [15]). Because of this, enormous amounts of air are needed for a controlled ventilation and, therefore, large capacities in the corresponding control unit (approx. 30,000 m3/h for a throughput of 1 t/h EPS).
The disposal (control) of pentane itself is achieved mainly through the following alternatives:
• Incineration
• Absorption
Incineration of the captured pentane emissions usually takes place in thermal oxidizers or in the steam boiler of the corresponding EPS processing facility.
Thermal oxidation is a procedure in which pentane is made to react with oxygen, producing carbon dioxide and water vapor. Pentane-laden air from a collecting line is introduced into a furnace (oxidizer) and heated up to temperatures of 750°C - 1200°C at which pentane is decomposed (burned) after a few seconds. The energy used to heat up the incoming air as well as the heat developed by the incineration of pentane can partly be recovered over an integrated air-to-air heat exchanger (recuperative thermal oxidation). In some cases this energy is used for steam generation; however, according to experience, with a low efficiency.
Thermal oxidation units represent a relatively high investment and cause, by the additional energy expenditure, high operating costs. Besides, with this kind of pentane disposal, additional greenhouse gases are given off.
The use of the facility’s existing steam boiler as control unit is discussed in detail below (see: 8. The "Epsilon system").
Occasionally, and only in connection with ventilated production buildings, gas turbines have been used as control units. The investment and operating cost of a gas turbine are very high and could be justified only through simultaneous use for generation of electric power (cogeneration).
Activated carbon beds have, among other things, been used for the absorption of pentane emissions. In this control alternative, pentane-laden air is introduced into suitable containers filled with activated carbon. Pentane is absorbed by the activated carbon. After a certain time, the absorptive capacity of the activated carbon is exhausted and the latter must be reactivated.
An absorption control system consists therefore of at least 2 absorption beds, which are operated and regenerated alternately. During reactivation (desorption with steam) the captured pentane is set free in concentrated form and must, thereafter, still be disposed of as a liquid. Control units working on the basis of absorption, are also expensive and have high operating costs.
This alternative does not require a special collecting mechanism to capture the emitted pentane, since all emissions can be caught in the (hermetic) production building. However, the pentane concentration may not exceed the max. allowable concentration in working areas (600 ppm, [15]). Because of this, enormous amounts of air are needed for a controlled ventilation and, therefore, large capacities in the corresponding control unit (approx. 30,000 m3/h for a throughput of 1 t/h EPS).
The disposal (control) of pentane itself is achieved mainly through the following alternatives:
• Incineration
• Absorption
Incineration of the captured pentane emissions usually takes place in thermal oxidizers or in the steam boiler of the corresponding EPS processing facility.
Thermal oxidation is a procedure in which pentane is made to react with oxygen, producing carbon dioxide and water vapor. Pentane-laden air from a collecting line is introduced into a furnace (oxidizer) and heated up to temperatures of 750°C - 1200°C at which pentane is decomposed (burned) after a few seconds. The energy used to heat up the incoming air as well as the heat developed by the incineration of pentane can partly be recovered over an integrated air-to-air heat exchanger (recuperative thermal oxidation). In some cases this energy is used for steam generation; however, according to experience, with a low efficiency.
Thermal oxidation units represent a relatively high investment and cause, by the additional energy expenditure, high operating costs. Besides, with this kind of pentane disposal, additional greenhouse gases are given off.
The use of the facility’s existing steam boiler as control unit is discussed in detail below (see: 8. The "Epsilon system").
Occasionally, and only in connection with ventilated production buildings, gas turbines have been used as control units. The investment and operating cost of a gas turbine are very high and could be justified only through simultaneous use for generation of electric power (cogeneration).
Activated carbon beds have, among other things, been used for the absorption of pentane emissions. In this control alternative, pentane-laden air is introduced into suitable containers filled with activated carbon. Pentane is absorbed by the activated carbon. After a certain time, the absorptive capacity of the activated carbon is exhausted and the latter must be reactivated.
An absorption control system consists therefore of at least 2 absorption beds, which are operated and regenerated alternately. During reactivation (desorption with steam) the captured pentane is set free in concentrated form and must, thereafter, still be disposed of as a liquid. Control units working on the basis of absorption, are also expensive and have high operating costs.
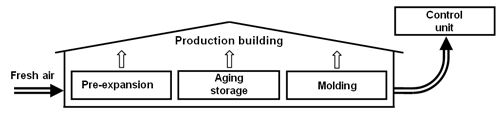
Fig. 3: Ventilated production building (schematic diagram).
8. The "Epsilon system".
The pentane emission control system developed by Epsilon Holdings since 1986 consists of a closed collection circuit (see Fig. 2), from which the combustion air for the steam boiler of the EPS processing facility is taken out. Thus the pentane in the collection circuit is disposed of in the burner of the steam boiler and replaces, by its heat of combustion, a corresponding amount (up to approx. 40%) of the conventional fuel of the steam boiler. At least 14 kg steam per kg of incinerated pentane can be produced in the steam boiler.
In order to achieve an optimal combustion of the pentane, the steam boiler must be outfitted with additional equipment and controls (see Fig. 4). Depending on the concentration of pentane in the combustion air taken out of the collection circuit, the supply of fuel is throttled. The concentration of the pentane in the collection circuit is controlled through suitable monitoring and safety devices and kept under 27 g/m3 (60% of the lower explosion limit [15]).
The pentane emission control system developed by Epsilon Holdings since 1986 consists of a closed collection circuit (see Fig. 2), from which the combustion air for the steam boiler of the EPS processing facility is taken out. Thus the pentane in the collection circuit is disposed of in the burner of the steam boiler and replaces, by its heat of combustion, a corresponding amount (up to approx. 40%) of the conventional fuel of the steam boiler. At least 14 kg steam per kg of incinerated pentane can be produced in the steam boiler.
In order to achieve an optimal combustion of the pentane, the steam boiler must be outfitted with additional equipment and controls (see Fig. 4). Depending on the concentration of pentane in the combustion air taken out of the collection circuit, the supply of fuel is throttled. The concentration of the pentane in the collection circuit is controlled through suitable monitoring and safety devices and kept under 27 g/m3 (60% of the lower explosion limit [15]).
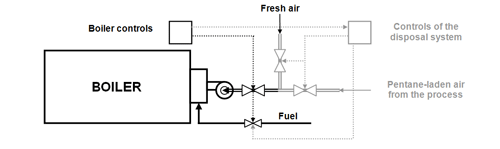
Fig. 4: Additional equipment & controls for the boiler in the "Epsilon System“
(drawn in grey; simplified schematic diagram).
9. Testing of pentane emission control systems.
Considering the variety of alternatives for control of pentane emissions in EPS processing plants, special care must be taken when testing such systems for delivery and/or approval.
The efficiency of a pentane emission control system can only be determined by means of a thorough test, which should take place under normal operating conditions and, if possible, over a period of 24 hours of the corresponding EPS processing facility.
The basic principle for testing any pentane emission control system is a material balance; i.e. determining, over a certain period, how much pentane was introduced with the EPS raw material into the process and how much pentane was actually disposed of in the control unit.
Determining how much pentane was brought in is relatively simple, since it can be calculated over the amount of EPS raw material used and its pentane content.
However, the data on pentane content of the supplied EPS raw material cannot always be relied upon. It is therefore advisable, when testing an emission control system, to determine the pentane content of samples of the raw material used in a well equipped and competent laboratory.
When testing an emission control system, all samples should be taken at least in triplicates, of which at least one series of samples is kept at the facility in a freezing compartment (if post-testing checks become necessary).
A recommendable method for the determination of the pentane content in a EPS sample (raw material or foamed material) is the method "SCAQMD Method 306-91" [19], published by the southern California air quality authority (South Coast Air Quality Management District).
In order to determine the pentane emitted during the foam manufacturing process, samples of the fresh finished product must also be taken and tested for their residual pentane content. It is very important that the samples taken actually contain (represent) the average pentane content of the fresh finished product (e.g. with EPS foam blocks).
Determination of how much pentane was disposed of, can only be done by a continuous measurement of the air flow entering into the control unit and the corresponding pentane concentration.
To determine the air flow, a suitable flow measuring instrument, which is inserted at the air inlet pipe of the control unit, can be used.
There are several suitable monitors available to measure the pentane concentration in the air flow. Normally, equipment with catalytic sensors and based on the principle of the heat of reaction of the samples taken, is sufficient for measuring and controlling the pentane concentration. For very precise measurements, devices based on the principle of flame ionization can be used. In all cases it is absolutely necessary that all these devices are previously calibrated with certified air-pentane gas mixtures, specially when carrying out any on-site tests.
The measured values for air flow and pentane concentration are recorded in regular intervals (e.g. every 15 sec). Based on these measured and recorded values, the amount of pentane that has flowed into the control unit during a given time can be calculated.
The relationship (in %) between the amount of pentane brought into the control unit and the amount of emitted pentane in the EPS process, represents the efficiency of the emission control system. Normally, efficiencies of 75 - 80% can be reached.
When testing a pentane emission control system, the efficiency of the control unit must also be determined. This is done, in the case of disposal by incineration, through an analysis of the exhaust gases of the thermal oxidizer, or the steam boiler. Efficiencies of 96-98% can be achieved with thermal oxidizers, while the efficiency with steam boilers is usually over 99%.
The efficiency of emission control systems based on the principle of absorption can be determined only over the resulting amount of desorbed liquid pentane.
10. Recommendations to the EPS processing industry.
• To the general public and the environmental authorities it should always be stressed with emphasis that the contribution of VOC emissions from the EPS processing is very small.
• It is foreseeable that the EPS industry in Europe will soon be required by the environmental authorities to control their VOC emissions; therefore, the topic "pentane disposal” should not remain, at least internally, unattended by any means.
• Eventual exaggerated official demands for the reduction of VOC emissions can be avoided through timely and voluntary actions in this direction.
• Internally, viable technical and economical guidelines for pentane emission control should be worked out immediately. These guidelines can serve, in given time, as a basis for environmental authorities to bring out appropriate regulations.
• Much attention should be paid to the fact that unqualified and opportunistic persons or companies remain excluded from any development connected to pentane emission control.
Bibliography
[1] Rogers P.: The Clean Air Act of 1970, EPA Journal - January/February 1990
http://www.epa.gov/history/topics/caa70/11.htm
[2] U.S. Environmental Protection Agency, Clean Air Act
http://www.epa.gov/air/oaq_caa.html/
[3] U.S. Environmental Protection Agency, National Ambient Air Quality Standards
http://www.epa.gov/air/criteria.html
{4] U.S. Environmental Protection Agency, Nonattainment Areas for Criteria Pollutants
http://www.epa.gov./oar/oaqps/greenbk/
[5] South Coast Air Quality Management District, RULE 1175
„Control of emissions from the manufacture of polymeric cellular (foam) products”
http://www.aqmd.gov/
[6] Confoederatio Helvetica, Systematische Sammlung des Bundesrechts
http://www.admin.ch/ch/d/sr/8/814.018.de.pdf
[7] European Environment Agency, Search: „COM(2000)613final“
http://www.eea.eu.int/main_html
[8] European Commission, Environment, Policies, Air, National Emission Ceilings Directive 2002/3/EC relating to ozone in ambient air
http://europa.eu.int/comm/environment/air/legis.htm#ceilings
[9] U.S. Environmental Protection Agency, Volatile Organic Compounds
http://www.epa.gov/airtrends/2005/pdfs/VOCNational.pdf
[10] Lidback, A., Chemical Market Associates, Inc.: Power-Point-Präsentation „Global EPS Market Review“, September 2004 S.28
[11] EUROSTAT, Environment and Energy, Tables, Long-term indicators – Environment, Environment and Energy, Environment, Air pollution and climate change, Emissions of non-methane volatile organic compounds
http://epp.eurostat.cec.eu.int/
[12] Chemical Market Associates, Inc., Global Plastics & Polymer Market Report, Issue No. 85 April 6, 2005 S. 32
[13] Snijders, E.A., Water Expandable Polystyrene, Technische Universiteit Eindhoven, 2003
[14] Wikipedia, The Free Encyclopedia
http://en.wikipedia.org/wiki/Pentane
http://en.wikipedia.org/wiki/Isopentane
http://en.wikipedia.org/wiki/Cyclopentane
[15] Baker, J.T., Material Safety Data Sheet
http://www.jtbaker.com/msds/englishhtml/p0737.htm
[16] Ohe, S., Vapor Pressure Calculation Program
http://www.s-ohe.com/Pentane_cal.html
[17] Chemistry Coach, 27.04.2004
http://www.chemistrycoach.com/vapor_pressure_of_water.htm
[18] Process Associates of America, Heat of Combustion of Fuel Gas
http://www.processassociates.com/Process/property/hc_gas.htm
[19] South Coast Air Quality Management District, Applied Science & Technology Division, Laboratory Services Branch, SCAQMD Method 306-91.pdf, Analysis of Pentanes in Expandable Styrene Polymers, Revised February 1993
Considering the variety of alternatives for control of pentane emissions in EPS processing plants, special care must be taken when testing such systems for delivery and/or approval.
The efficiency of a pentane emission control system can only be determined by means of a thorough test, which should take place under normal operating conditions and, if possible, over a period of 24 hours of the corresponding EPS processing facility.
The basic principle for testing any pentane emission control system is a material balance; i.e. determining, over a certain period, how much pentane was introduced with the EPS raw material into the process and how much pentane was actually disposed of in the control unit.
Determining how much pentane was brought in is relatively simple, since it can be calculated over the amount of EPS raw material used and its pentane content.
However, the data on pentane content of the supplied EPS raw material cannot always be relied upon. It is therefore advisable, when testing an emission control system, to determine the pentane content of samples of the raw material used in a well equipped and competent laboratory.
When testing an emission control system, all samples should be taken at least in triplicates, of which at least one series of samples is kept at the facility in a freezing compartment (if post-testing checks become necessary).
A recommendable method for the determination of the pentane content in a EPS sample (raw material or foamed material) is the method "SCAQMD Method 306-91" [19], published by the southern California air quality authority (South Coast Air Quality Management District).
In order to determine the pentane emitted during the foam manufacturing process, samples of the fresh finished product must also be taken and tested for their residual pentane content. It is very important that the samples taken actually contain (represent) the average pentane content of the fresh finished product (e.g. with EPS foam blocks).
Determination of how much pentane was disposed of, can only be done by a continuous measurement of the air flow entering into the control unit and the corresponding pentane concentration.
To determine the air flow, a suitable flow measuring instrument, which is inserted at the air inlet pipe of the control unit, can be used.
There are several suitable monitors available to measure the pentane concentration in the air flow. Normally, equipment with catalytic sensors and based on the principle of the heat of reaction of the samples taken, is sufficient for measuring and controlling the pentane concentration. For very precise measurements, devices based on the principle of flame ionization can be used. In all cases it is absolutely necessary that all these devices are previously calibrated with certified air-pentane gas mixtures, specially when carrying out any on-site tests.
The measured values for air flow and pentane concentration are recorded in regular intervals (e.g. every 15 sec). Based on these measured and recorded values, the amount of pentane that has flowed into the control unit during a given time can be calculated.
The relationship (in %) between the amount of pentane brought into the control unit and the amount of emitted pentane in the EPS process, represents the efficiency of the emission control system. Normally, efficiencies of 75 - 80% can be reached.
When testing a pentane emission control system, the efficiency of the control unit must also be determined. This is done, in the case of disposal by incineration, through an analysis of the exhaust gases of the thermal oxidizer, or the steam boiler. Efficiencies of 96-98% can be achieved with thermal oxidizers, while the efficiency with steam boilers is usually over 99%.
The efficiency of emission control systems based on the principle of absorption can be determined only over the resulting amount of desorbed liquid pentane.
10. Recommendations to the EPS processing industry.
• To the general public and the environmental authorities it should always be stressed with emphasis that the contribution of VOC emissions from the EPS processing is very small.
• It is foreseeable that the EPS industry in Europe will soon be required by the environmental authorities to control their VOC emissions; therefore, the topic "pentane disposal” should not remain, at least internally, unattended by any means.
• Eventual exaggerated official demands for the reduction of VOC emissions can be avoided through timely and voluntary actions in this direction.
• Internally, viable technical and economical guidelines for pentane emission control should be worked out immediately. These guidelines can serve, in given time, as a basis for environmental authorities to bring out appropriate regulations.
• Much attention should be paid to the fact that unqualified and opportunistic persons or companies remain excluded from any development connected to pentane emission control.
Bibliography
[1] Rogers P.: The Clean Air Act of 1970, EPA Journal - January/February 1990
http://www.epa.gov/history/topics/caa70/11.htm
[2] U.S. Environmental Protection Agency, Clean Air Act
http://www.epa.gov/air/oaq_caa.html/
[3] U.S. Environmental Protection Agency, National Ambient Air Quality Standards
http://www.epa.gov/air/criteria.html
{4] U.S. Environmental Protection Agency, Nonattainment Areas for Criteria Pollutants
http://www.epa.gov./oar/oaqps/greenbk/
[5] South Coast Air Quality Management District, RULE 1175
„Control of emissions from the manufacture of polymeric cellular (foam) products”
http://www.aqmd.gov/
[6] Confoederatio Helvetica, Systematische Sammlung des Bundesrechts
http://www.admin.ch/ch/d/sr/8/814.018.de.pdf
[7] European Environment Agency, Search: „COM(2000)613final“
http://www.eea.eu.int/main_html
[8] European Commission, Environment, Policies, Air, National Emission Ceilings Directive 2002/3/EC relating to ozone in ambient air
http://europa.eu.int/comm/environment/air/legis.htm#ceilings
[9] U.S. Environmental Protection Agency, Volatile Organic Compounds
http://www.epa.gov/airtrends/2005/pdfs/VOCNational.pdf
[10] Lidback, A., Chemical Market Associates, Inc.: Power-Point-Präsentation „Global EPS Market Review“, September 2004 S.28
[11] EUROSTAT, Environment and Energy, Tables, Long-term indicators – Environment, Environment and Energy, Environment, Air pollution and climate change, Emissions of non-methane volatile organic compounds
http://epp.eurostat.cec.eu.int/
[12] Chemical Market Associates, Inc., Global Plastics & Polymer Market Report, Issue No. 85 April 6, 2005 S. 32
[13] Snijders, E.A., Water Expandable Polystyrene, Technische Universiteit Eindhoven, 2003
[14] Wikipedia, The Free Encyclopedia
http://en.wikipedia.org/wiki/Pentane
http://en.wikipedia.org/wiki/Isopentane
http://en.wikipedia.org/wiki/Cyclopentane
[15] Baker, J.T., Material Safety Data Sheet
http://www.jtbaker.com/msds/englishhtml/p0737.htm
[16] Ohe, S., Vapor Pressure Calculation Program
http://www.s-ohe.com/Pentane_cal.html
[17] Chemistry Coach, 27.04.2004
http://www.chemistrycoach.com/vapor_pressure_of_water.htm
[18] Process Associates of America, Heat of Combustion of Fuel Gas
http://www.processassociates.com/Process/property/hc_gas.htm
[19] South Coast Air Quality Management District, Applied Science & Technology Division, Laboratory Services Branch, SCAQMD Method 306-91.pdf, Analysis of Pentanes in Expandable Styrene Polymers, Revised February 1993

